diy autoclave composites|composite autoclave for sale : distributors 1000 Litre (250 Gallon) Autoclave: I made this large sterilizer for mushroom culture, but it could also be used for composite part layup. It was a fast build and there is some danger, so read . Designed to preserve the eficiency of the autoclave and avoid deterioration caused by limestone, the conductivity sensor checks the quality of the inlet water in order to guarantee correct .
{plog:ftitle_list}
Distributor Alat Kedokteran Indonesia menjual Steam Sterilizer, sterilisator atau autoclave dengan spesifikasi yang lengkap. alat ini berfungsi sebagai alat yang digunakan untuk mensterilisasi alat alat medis.
A composite autoclave is a closed moulding tool/oven that uses pressurised steam to manufacture lightweight and strong composite materials. Autoclave curing creates a high .
1000 Litre (250 Gallon) Autoclave: I made this large sterilizer for mushroom culture, but it could also be used for composite part layup. It was a fast build and there is some danger, so read .
In the video we demonstrate how to duplicate a small existing component using our highly effective XC110 'out-of-autoclave' carbon fibre prepreg.
Buying or building an oven for curing composite prepregs or postcuring composite parts. Details about structure, heaters, monitoring and safety. . For all but the best and most well designed “DIY” ovens, it is always . Autoclave curing relies on a combination of temperature and pressure to consolidate resin and fabric. High performance parts are typically cured in an autoclave. Thus, the advantages of vacuum bagging are diminished. With vacuum bagging, you also generate waste. Vacuum bagging is a great practice for DIY fabricators. We choose autoclave composites over OOA composites to deliver perfection. Traditional high pressure autoclaves have always been popular for manufacturing carbon fiber prepreg composites, as widely used in the aerospace industry.Out Of Autoclave (OOA) has been around for some time as an alternative process but a drawback is that it does not deliver the .ASC's composites autoclaves are designed to provide the quickest turnaround for each production load of composite parts. Production cycle times are directly dependent on ability of the autoclave to transfer thermal energy into the part and tool load. This transfer can be improved by high air-speeds and uniform flow within the autoclave environment.
Easy Composites Ltd – Beginners’ Guide to Out of Autoclave Carbon Fibre Page 4 of 21 Materials & Equipment To ensure the best possible results from your out-of-autoclave prepreg carbon fibre we will be using carefully selected products from the Easy Composites range. Most prepregs are intended for curing at very high pressure in an #diy #composites #carbonfiber #carbon #autoclave #motorcycle #automobile#carbonfiber #diy #sbk #bmw #carbonparts #bike #frp #forgedcarbon
Composite materials have gained increased usage due to their unique characteristic of a high-stiffness-to-weight ratio. High-performing composite materials are produced in the autoclave by applying elevated pressure and temperature. However, the process is characterized by numerous disadvantages, such as long cycle time, massive investment, . Discover how Multi-Ply, a leading composite parts manufacturer, revolutionized composite production planning with Plataine’s AI-powered solution. This webinar will detail how an AI scheduling solution, designed for composite manufacturing, minimizes delays, optimizes resource allocation and drives higher throughput. Autoclave curing relies on a combination of temperature and pressure to consolidate resin and fabric. High performance parts are typically cured in an autoclave. Thus, the advantages of vacuum bagging are diminished. With vacuum bagging, you also generate waste. Vacuum bagging is a great practice for DIY fabricators.
Our composite autoclaves follow the highest possible standards in quality construction. All our vacuum system tubing is stainless-steel in design and is standardized on all composite autoclaves. Our systems are constructed within multiple international standards in mind, including (but not limited to) ASME, UL, CE/PED, and others.Video tutorial explaining the basics of diy carbon fibre sheet production followed by practical advice on three manufacturing techniques; wet-layup, resin infusion and prepreg laminating. . A single laminate sample is prepared using a layer of our old Easy-Preg out-of-autoclave surfacing prepreg top and bottom with three layers of our old . Also don’t count on your molds lasting more than a few cooks – especially if you are autoclave curing. . While most of this article focuses on CNC machining MDF to make composites tooling, it is also a very versatile material for hand-built tooling. MDF is designed to build low-cost finished furniture and cabinetry and to give nice shiny .Composite materials, such as carbon fiber reinforced plastics are highly versatile and efficient materials, driving innovation in various markets from aerospace to healthcare. They outperform traditional materials such as steel, aluminum, wood, or plastic, and enable the fabrication of high-performance lightweight products.
domina plus b autoclave istruzioni
The XC110 Pre-preg is specially designed to be processed out of autoclave under vacuum in an oven and thus would give much better surface results than a typical autoclave pre-preg processed in this way. The first stage is to make accurate templates. The quickest and easiest way to do this is to use masking tape. Pre-preg and autoclaves arnt really something that has been used in home building before you have to understand that this is the latest technology in composites and is usually only used in high end motorsport and aerospace the costs for this kinda thing are normally huge (autoclaves cost a LOT of money)
A primer on the reasons to use vacuum bagging in composite part manufacture, and the basics of how to do it. Advertisement Connecting the composites industry . in an autoclave cure, much higher pressures are routinely available, up to several hundred psi for some types of solid laminates. However, the vacuum bag is still required in these .
This year however we don't have access to an industrial oven/autoclave, and we are (desperately) thinking of making our own. We have a fairly decent budget (not enough to buy an industrial oven ourselves tho). However we don't have a lot of hands on experience in oven making. Are there any good resources/DIY guides on that?
domina plus b autoclave manuale
#carbonfiber #airscoop #moldHow to Make a Carbon Fiber Parts Clone [DIY] (Making Mold & Air Scoop)How to Make a Carbon Fiber Parts ReplicaMaking a Carbon Fib.Out of autoclave composite manufacturing is an alternative to the traditional high pressure autoclave (industrial) curing process commonly used by the aerospace manufacturers for manufacturing composite material.Out of autoclave (OOA) is a process that achieves the same quality as an autoclave but through a different process. [1] OOA curing achieves the desired .Composite Curing Ovens. Large Composite Curing Ovens by ASC. We design, engineer, & manufacture carbon fiber composite curing ovens. Although there are a number of companies that build ovens, ASC Process Systems is the only company that can design, manufacture, and ship a factory-complete composite curing oven system with state-of-the-art features, capabilities, and .since, there are not autoclaves large enough to process 9-10 meter composite shells. Therefore, OOA composites are an excellent alternative to autoclaved composite structures. Recent advances in composite automated manufacturing technologies will be required to mitigate out-life (OL) and tack-life of prepreg for large composites.
What Is a Composite Autoclave & How Does It Work? Pros and Cons. Composite autoclaves are essential in fabricating high-tech products like carbon fiber for different industry sectors. These specialized devices are very important because to achieve lightweight and high strength and durability of the final product required for aerospace, automotive and sports equipment industries.Benefits of using autoclave curing composites. Using Element’s composite curing autoclaves for R&D and quality assurance allows our customers to optimize the use of their in-house autoclaves for manufacturing purposes. To create the most optimal composite products, autoclave curing is essential during R&D and manufacturing processes.The ASC Process Systems Econoclave ® is the world's most popular composite curing autoclave. It brings together unique ASC design, quality materials, advanced capabilities, and streamlined manufacturing to provide an affordable, energy savings, aerospace-grade autoclave for Tier I, II, and III manufacturers. . energy savings, aerospace-grade .Autoclave means added pressure as well. Without pressure it's just an oven cure. But room temp curing resins and vacuum bagging is good enough for any DIY stuff. Even the aerospace industry is trying to get away from autoclaves.
used composite autoclaves for sale
Alternatives to Autoclave Methods: Although autoclave molding can produce high-performance composites, the exploration of alternatives outside the autoclave highlights the need for more cost-effective and efficient manufacturing methods that can achieve similar quality without facing the challenges associated with autoclave molding.
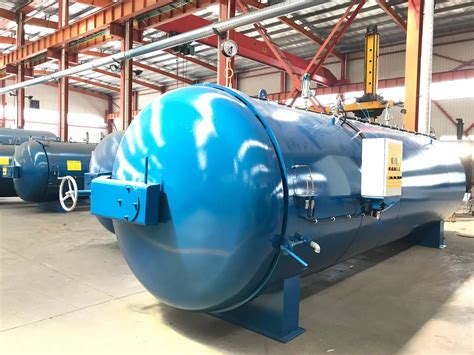
out of autoclave composite manufacturing
domina plus b autoclave manuale italiano
Ball and poppet are an integral design to assure positive, in-line seating without “chatter”. Poppet is designed essentially for axial flow with minimum pressure drop. Minimum operating .
diy autoclave composites|composite autoclave for sale